The Durability Test
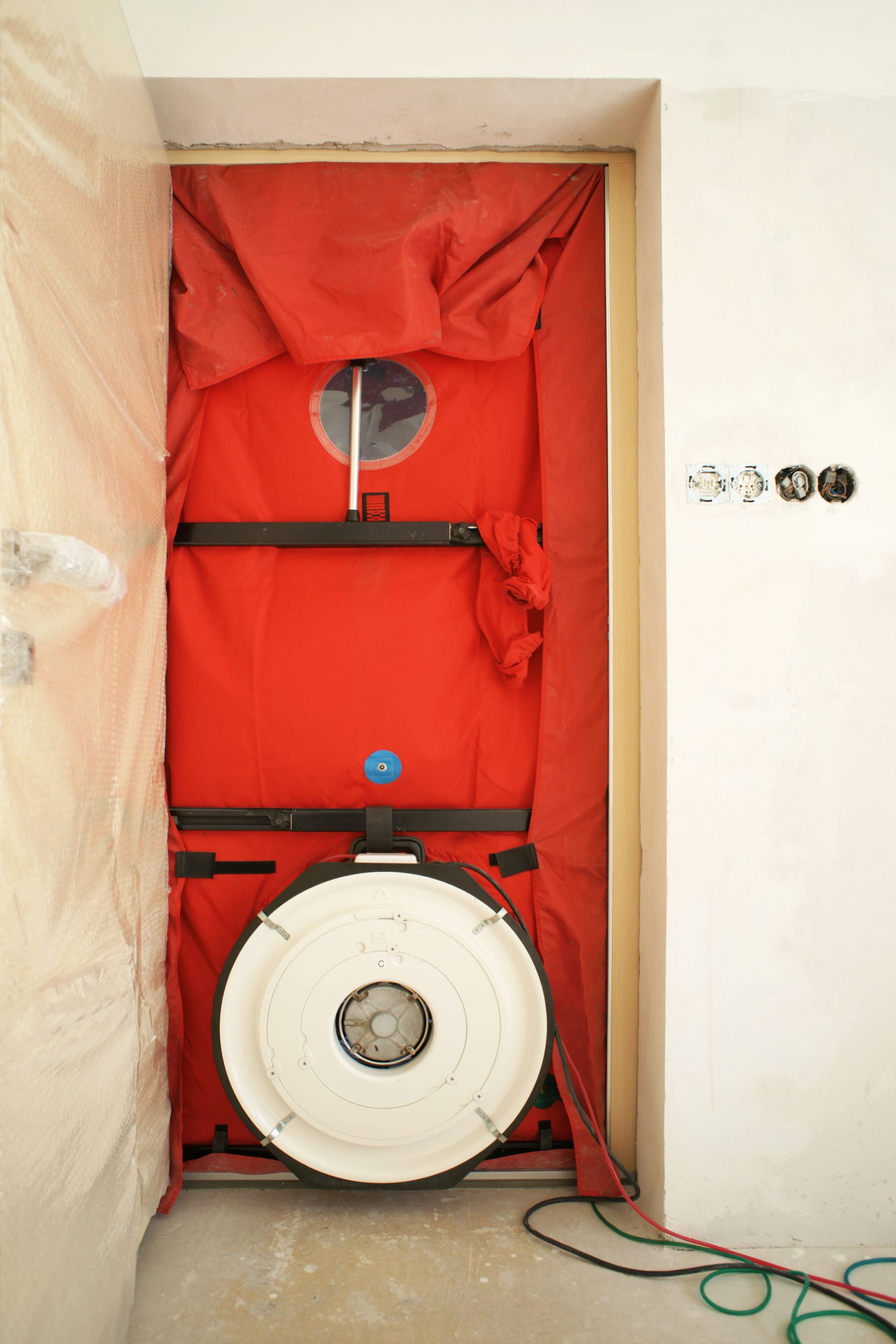
The Blower Door Test: A Key to Durability in High-Performance Homes
While a blower door test is most commonly associated with measuring air leakage in a home’s envelope, at Kala, we also see it as crucial for ensuring durability. The connection between air leakage and water intrusion is significant—if your home leaks air, it will leak water. This can occur either through bulk water entering gaps in the envelope or through water vapor becoming trapped within the wall assembly. Both scenarios can lead to serious durability issues, such as moisture buildup, mold growth, wood rot, and structural damage.
What is a Blower Door Test?
A blower door test is a method used to measure the airtightness of a building. It involves placing a powerful fan in a door opening, which either pressurizes or depressurizes the house. This process allows professionals to identify the rate at which air leaks in and out of the home, typically measured by ACH50—Air Changes per Hour at 50 Pascals. This metric indicates how many times the air inside a building is replaced within an hour when the building is pressurized to 50 Pascals. Higher values indicate a leakier house.
Setting the Air Leakage Standard
Before Kansas City, Missouri adopted the 2021 International Energy Conservation Code (IECC), there was no code requirement for a maximum number of air changes per hour (ACH) in new construction. The 2021 IECC now sets a maximum of 3 ACH50 for all new homes though Kansas City, Missouri is the only jurisdiction that has adopted 2021 IECC. The rest of the metro area does not have any sort of blower door test or air changes per hour requirement to meet code.
At Kala, we strive to build homes that achieve 1 ACH50 or below. To attain certification from the Passive House Institute of the US (Phius), a home must meet an even stricter standard of 0.6 ACH50 or lower.
We compiled data from our five most recent custom home builds, and our air tightness levels range from well below the Phius standard to just about 1 ACH50. These homes vary in size and finishes, but each one is verified airtight:
- South Olathe New Custom Home: 0.85 ACH50
- Beacon Hill Passive House: 0.36 ACH50
- Rural Farmhouse: 0.42 ACH50
- Prairie Village Custom Home: 0.63 ACH50
- Westwood Performance Home: 1.03 ACH50
Why is Air Tightness a Concern?
So, these houses are all built to be super airtight, but why does that matter? How does air cause damage? All great questions.
To understand why air intrusion matters when building a home, it helps to quantify the amount of water vapor present in the air. In Kansas City, relative humidity averages around 60-66% throughout the year, and you can expect an average day in July to reach about 81°F. At this temperature and humidity level, the air can hold a significant amount of moisture—approximately 0.4 to 0.6 grams of water per cubic foot. As this humid air infiltrates a poorly sealed home, it carries that moisture into the wall assembly. For example, air leakage through a small, 1-square-inch hole in a building’s envelope during the heating season can result in approximately 28.4 liters (30 quarts) of water being transmitted to the interior. This moisture can condense, particularly when it comes into contact with cooler surfaces inside the wall, leading to water accumulation. Over time, this trapped moisture can cause rot, mold growth, and structural damage, significantly reducing the durability of the building.
Air Sealing the Building Envelope
In an article for Green Building Advisor, inspector Randy Williams suggested, “The best approach to passing a blower-door test is to understand where houses leak air and design an air-sealing strategy with that in mind.” At Kala, we take this mandate very seriously.
Windows and doors are common sites of excess air leakage. To prevent this, we use high performance windows that meet air tightness requirements. It's equally important that the windows are installed by trained professionals to keep the space around the frame of the window air and water tight.
It's important to minimize outside air coming in and inside air leaking out. Outside air is significant because pollutants, allergens, and toxins often creep into your home through small cracks and holes throughout.
In a home built with typical construction methods, air can pass in and out through the building envelope. This doesn’t happen in a high-performance home because air and vapor layers are thoughtfully placed in the wall assembly, preventing excessive airflow and leakage. Once air is contained, it can be controlled, allowing you to maintain a consistent temperature and humidity level in all seasons.
Another area that we pay particular attention to during the building process is the roof/attic cavity. This area is often a significant source of air leakage in many houses, as air passes both ways through the ceiling and into or out of the living space below. To prevent this, Passive House builders pay special attention to this area, ensuring the structure is airtight with continuous insulation around all living spaces.
In addition to using a top-down approach to air management, we also take a close look from the ground up. Another common fail point for air and moisture intrusion in a home is at the mudsill, where the foundation meets the exterior walls. We apply two extra beads of caulking above the foundation wall before the sill sealer to prevent any airflow at this connection. This is such a simple task that will pay dividends in the long run.
Fresh, Filtered Air In, Stale Air Out
Combined with an airtight envelope, the use of an ERV system ensures that only clean, fresh, filtered air is brought into a Passive House, while stale air is constantly removed. In older homes you are getting “fresh” air through those cracks and holes in the envelope, but when you build a Passive House you have to manually bring fresh air. This is accomplished through the ERV system.
Mid-Construction Testing and Verification
Whether we are certifying a home or not, we pay careful attention to ensure every home with our name on it is effectively sealed. A blower door test is conducted on every home we build post rough-in to find the source of any leaks. We also test the ERV system and even monitor airflow at each vent and return. All of this provides peace of mind that the indoor environment will be healthy and safe, and that the air and moisture buildup often leading to costly durability issues in regular houses won’t be a problem.
High-performance homes are often associated with energy efficiency, and for good reason. But the benefits of building better homes go far beyond using energy wisely. Yes, you’ll pay less to heat and cool your home, but you’ll also pay much less in maintenance costs due to the care taken in air sealing throughout the construction process.